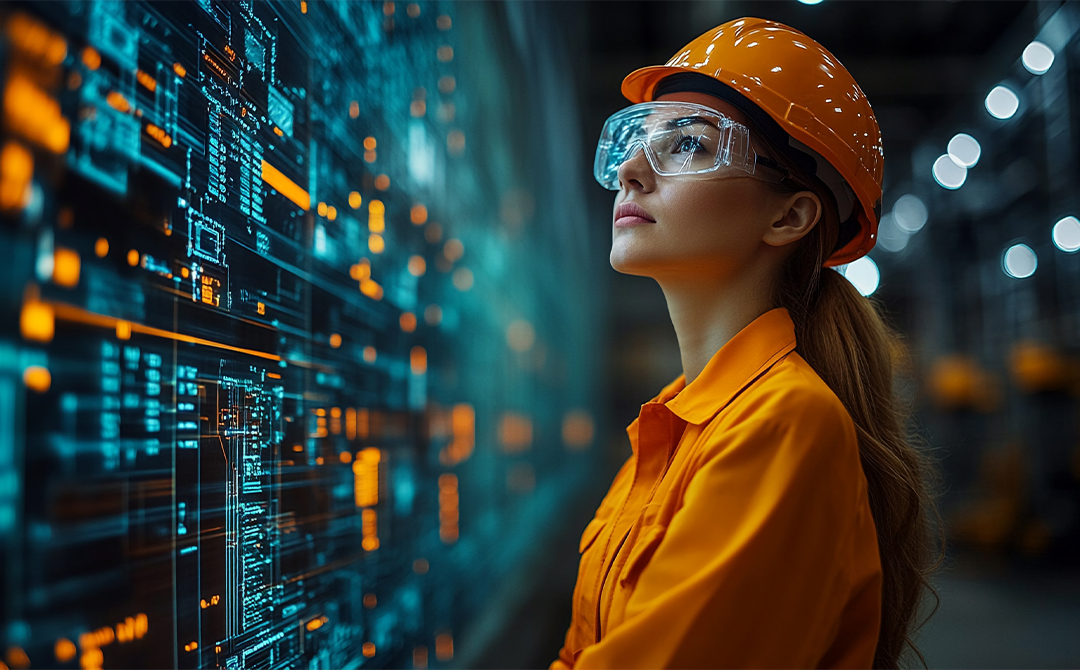
Manufacturers worldwide face mounting pressure to optimize operations amid talent shortages, supply chain disruptions, and rising costs. According to a January 2024 McKinsey report, unplanned downtime costs Fortune Global 500 manufacturers roughly $1.5 trillion annually, about 11% of their turnover. In fast-moving industries, a single minute production line stoppage can cost millions of dollars.
The global digital twin market is growing explosively. Zion Market Research projects the digital twins in the manufacturing market will surge from approximately $10.27 billion in 2023 to $714 billion by 2032, representing a compound annual growth rate (CAGR) of over 60% between 2024 and 2032. This rapid growth underscores the critical role digital twins play in addressing these operational challenges.
Moreover, McKinsey’s 2022 survey found that 86% of industrial executives see digital twins as applicable to their operations, with 44% already implementing them and 15% planning deployment soon.
Why This Is a Huge Problem: Impact on Business
According to a Siemens report, "The True Cost of Downtime 2022," Fortune Global 500 companies collectively incur an estimated $1.5 trillion in annual losses due to unplanned downtime, representing 11% of their yearly turnover In high-volume environments like the automotive industry, a mere minute of production line stoppage can cost an astounding $2 million.
Source: Siemens - THE TRUE COST OF DOWNTIME 2022 Report
Operational inefficiencies such as unplanned downtime, poor scheduling, and lack of real-time visibility cause costly production delays and quality issues. These directly affect revenue, customer satisfaction, and competitive positioning. For example, McKinsey highlights that digital twins enable predictive maintenance, which can reduce maintenance costs by up to 40% and increase asset uptime by 5–10%, creating significant cost savings and operational resilience.
Deeper Insight: Global Business, Industry, and Technology Challenges
- Business Challenges: Heightened competition, volatile demand, and supply chain disruptions require agility and cost efficiency.
- Industry Challenges: Legacy systems, siloed data, and manual processes impede innovation and rapid decision-making.
- Technology Challenges: Integrating IT and OT data, ensuring cybersecurity, and extracting actionable insights remain complex.
As per Mckinsey report, these are top challenges collectively hinder industrial productivity and growth.
Digital Twins: The Solution to Industrial Complexity
Digital twins are real-time virtual replicas of physical assets, processes, or entire factories, continuously fed with live data from IoT sensors, MES, ERP, and other systems. They enable:
- Real-Time Monitoring & Diagnostics: Immediate anomaly detection and performance tracking.
- Predictive & Prescriptive Analytics: AI-driven insights for proactive maintenance and process optimization.
- Scenario Simulation: “What-if” analyses to evaluate operational changes without disruption.
- End-to-End Optimization: Integration across assets and supply chain nodes for holistic decision-making.
McKinsey reports that digital twins can accelerate product development by up to 50%, improve product quality by 25%, and increase revenue by 10%.
Why Solving This Problem Matters
Industrial leaders that adopt digital twins can unlock significant competitive advantages. Boston Consulting Group research shows companies with successful digital transformations, including digital twins, achieve earnings growth 1.8 times higher than peers
Business Impact: Real-World Examples from Tredence
- Digital Twin for Weld Job Quality Prediction for a Large Welding Industry Player
Integrated robotic weld machines with a cloud-based streaming and batch data architecture. Deployed anomaly detection and root cause analysis models to identify factors impacting weld quality. Enabled operations teams to prioritize anomalies effectively.
Business Impact: ~ 17% reduction in quality defects.
- Digital twin for Prescriptive Machine Settings for a Global Aluminum Sheets Manufacturer
Developed models for quality prediction and machine settings recommendations, deployed at the plant edge for sub-second latency insights. Managed a feature store handling 10,000 new features per batch.
Business Impact: Reduced production stoppages by around 23%.
- Digital twin for Batch Quality Prediction and Optimizer for a Global Cement Major
Developed machine learning models to predict cement setting strength using production and lab test data. Enabled operators to optimize production parameters, reducing over- and under-quality batches.
Business Impact: Improved batch quality by 10%.
Tredence Digital Twins: Definition, USP, and Accelerators
At Tredence, we define digital twins as dynamic, data-driven models that unlock the value of data and AI—extending beyond monitoring to enable smart diagnostics and next-best actions.
Types of Digital Twins Delivered
- Product/Asset Twins: Analyze component connectivity and predict operational performance.
- System/Unit Twins: Monitor interactions within interdependent subsystems.
- Operational Twins: Optimize end-to-end processes for efficiency and risk reduction.
What Sets Tredence Apart
Classical Digital Twins |
Tredence Digital Twins |
Physics/simulated data for engineering |
Real-time monitoring & diagnostics of complex processes |
Simulated data for SOPs |
Enterprise & live streaming data, real-time anomaly detection |
Siloed, asset-focused applications |
Extendable ecosystem integrating BI & AI |
Asset FMEA/specs |
Combine Asset & Process FMEA with analytics for real-time insights |
Design/engineering focus |
Operations & digital teams, edge integration, digital solution building |
Four Key Accelerators Powering Tredence Digital Twins
To accelerate digital twin development with lightning speed and address critical industrial features, Tredence offers four prebuilt accelerators:
- OT & IT Connected Data Model & KPIs
Notebooks integrating SAP master and transaction data with OT counters and sensor data, plus a precalculated KPI library for unified insights. - Knowledge Graph
Built with open-source graph libraries enabling traceability across assets, processes, and events. - AI/ML Accelerators
Ready-to-use AI/ML modules for alerting, root cause analysis, predictive and prescriptive analytics, and digital assistance. - UI/UX Frameworks
Pre-built UI/UX templates accelerate the design of intuitive dashboards to consume manufacturing digital twin insights.
These accelerators enable rapid deployment, scalability, and comprehensive feature coverage.
Digital twins are essential for industrial transformation. Tredence’s differentiated approach, powered by our accelerators, unlocks operational excellence, cost savings, and sustainable growth aimed towards delivering impactful working capital management systems.
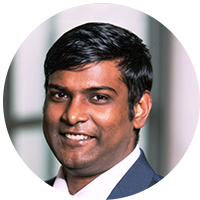
AUTHOR - FOLLOW
Aritro Ghosh
Manager, Supply Chain Management
Next Topic
How to scope a Unity Catalog (UC) Workflow Migration using System Tables
Next Topic